
Recapturing the Golden Period
My deep belief that the Old Italian makers in the 17th and 18th century used a different material to create a string instruments in Italy, in contrast to those in the rest of Europe in their time, and to the rest of the world, including Italy, in our time.
Such a statement may reinforce many makers believe, that the material (means the wood) available at that particular time and place in history was of a superior quality to that which we have now. In other words, to make great instruments on a par with Strad or Bergonzi today are impossible.
It gives the biggest excuse to the many. But to see the wood by itself only as a material, but not as a part of it, was and it is a short vision, lacking in logic and common sense.
As we know, wood is a porous and absorbent material, and by adding any substance to the wood we change its molecular structure.
So, in the making of a violin, we apply varnish to cover the raw wood. This protects it from atmospheric conditions and combats physical deterioration.
Depending on the type and the quality of the varnish and the application procedure, combined with the wood, will create a variety of the different materials.
Oil or alcohol based varnish or anything in between, or hard, medium or soft varnish, in combination with the wood, will create the material that would let the violin to vibrate differently. Since the violin is an acoustical box, an amplifier, different model, arching and material its made from, will react differently, creating a sound we all familiar with from the past, or modern version of today.
The ignorance of many, not seeing the obvious, the laziness of others to keep the status quo, the never ending mystery and secret searching that does not exist, prevent them from rediscovering the past and starting from the point when history was interrupted.

The Interrupted History of Violin Making
The year 1780 saw the end of an era of remarkable advances in the luthiers’ craft, which achieved its apotheosis in the instruments produced by Stradivarius and Guarneri family. These Italian master craftsmen had produced instruments of astoundingly beautiful tone and total responsiveness. They had improved upon the shape of the violin; in so doing, they had defined the parameters of arching and its optimal relationship to overall shape and size. In addition, they had developed natural varnishes which, when applied to these finely crafted instruments, not only accentuated their superior qualities, but enabled these qualities to improve over time.
It seemed that the stage had been set for future generations of violin makers to produce their own wonderful instruments, based upon techniques which were widely used by the Italian masters. As far as anyone could expect, luthiers would continue their noble tradition. The fact is that this did not occur , and the history of fine violin making was interrupted.
Mystery, Secret – or A Simple Fact of Broken Tradition?
Let us analyze a few factors which may help us understand why the “OLD ITALIANS” made such good instruments, and why the golden period was followed by decay.
In my mind, only three factors make a Stradivarius a Stradivarius , or a Gagliano a Gagliano. Three factors area: OUTLINE(model), ARCHING and VARNISH.
Other factors play supporting, but not critical,roles. What are the differences among the various Italian schools: Cremonese, Napolitan, Venetian, or Brescian? The most important differences are the three aforementioned: outline, arching, varnish. All of these in combination make a difference in the sound. Even the dissimilarities between, say , earlie and later Strads, are due to these factors, which gave these instruments their distinctive sounds.
To support my point, let’s take a look at the instruments they left for us. Some of the best-sounding instruments, particularly cellos, are made from the worst wood, which would never have been considered by modern violinmakers. The old masters should have been ashamed to glue together six pieces of maple and carve a back, or use all knotted spruce (perhaps only good enough to make a picket fence out of ) and build a top from it. Or worse, to use two very different pieces of poplar wood that were so cheap it wouldn’t have made any sense to cut them even for profit.
Yet these were partially the building blocks used by the great masters. Where did they get this horrible poplar wood? Locally, without a doubt. And what about the story that the secret of the sound of the old instruments lies in wood exposed to salt and bacteria as it floated by sea to Italy from other countries? Can you imagine those poor luthiers sending this poplar wood, unusable even as firewood, to Turkey and back just to get the same salty result? Isn’t this proof that wood is just a material? You need only a soft and a hard wood to build a violin, and practically any kind for a cello.
The top and back of the instrument needed to be strong, supportive and flexible at the same time, with thickness
logically determined. Contrary to some popular notions, there is no secret tuning to be discovered. Of the three most important factors affecting sound, varnish plays an enormous role in creating or destroying it.
Didn’t everyone, then, know the rules and techniques for building an instrument? Wouldn’t they, in large part, have been influenced by Amati and then by Stradivarius? Couldn’t they build the same quality instruments? In fact, they had the same “secret” wood. Many used the same model, with similar arching. One thing was different: they didn’t have the same varnish.

The conventional way...

My technique using NO Alcohol, NO Oil and NO Pigment via a proprietary cooking process
Reinventing The Wheel
The future of violin making lies in understanding its past history. Can we retrace history and perfectly reproduce the varnish and application system the old Italian masters used? It’s practically an impossible task. We don’t have the same quality of resins, nor do we know the recipe ingredients or proportions they used. We do know for a fact, that no Italian violinmaker than, ever painted his instruments in blue, green, or zebra stripes. Presumably there were enough of all kinds of pigments then, or enough tasteless customers to influence the makers’ taste.
The color that all violin makers used, without exception from the very early sixteenth century to the very late eighteenth century, was red: from light golden red to dark brown red. Was it accidental, or the way the varnish was made, that couldn’t lead to any other result? By analyzing the best existing examples of their creations, trying to implement a new approach based on an idea that the varnish used by the Italian masters was pigment free. I came upon unexpected results that can finally bring to an end an infinite dispute among violinmakers about whether the base of varnish should be oil or alcohol.
What is the biggest variable among the Italian schools, or among the several other national schools: French, German, English and Czech? Varnish. What is the major difference among 18th, 19th, 20th century? It is not corners, F holes, or purflings, it’s varnish. An old instrument, which has been stripped of its original varnish and coated by modern varnish has lost a critical part. The sound is changed; authentication is very difficult or impossible; and its value is drastically diminished.
Different Italian varnishes, and the sounds associated with them, are characterized and designated by its place of origin, such as Cremonese, Venetian, Neapolitan. The varnish on instruments of makers who moved around and worked in different places reflects these different characteristics. But varnishes in Italy during the golden period of violin- making also had enough in common to give rise to the fame of “Italian” varnish and the sound associated with it. French, German or English varnish was different, each with its own unmistakable identity. Italian luthier, Vincenzo Panormo, who went to England, became English violinmaker with a related sound; similarly with German violinmakers, who moved to Italy, as with Matteo Goffriller, who moved to Venice, and became an Italian violinmaker, and developed an unmistakably Venetian sound.
Why, then, did the quality of violin sound diminish, nearly all at once, all over Italy? This occurred when a new varnish was introduced, replacing the old “cooking” process that produced a great deal of smoke, and which could only have been carried out outside of the cities. It was produced on a large scale and sold to individual violinmakers. The new varnish, introduced during the late eighteenth century, was much easier to manufacture using household facilities.
Regrettably, over time, it was simplified even more into the process of dissolving resins and pigment in alcohol, which evaporates after approximately six months. This varnish literally left violins sealed within hard resins. It made instruments sound harsh and flat, with few overtones, and little of the warmth and beauty of the “old Italians”.
The “ cooking “ process used by the old Italian masters transformed natural resins into the incomparable varnish of Stradivarius. When this method disappeared, so did the production of fine instruments. Thus, two hundred years ago, violin makers opted for what they perceived as progress, unwittingly leaving behind the most important part in the tradition of violin making - suitable varnish.
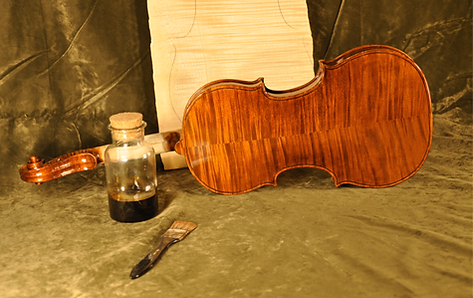
After many years of intensive research and experiments, a pigment free varnish made by a “ very simple cooking process “ using neither alcohol nor oil bases was found, to have a beautiful natural red color. Depending on the kind and quality of resins, the time and temperature of cooking, and the eventual penetration into different woods by the application process, the resultant color varies from light golden red to dark reddish brown.
A new-varnished violin is dry and ready to be played on in two weeks, but the instrument will never be encased in a hard layer of varnish, which stunts the sound. Ideally, when dry it remains soft, allowing for a free response similar to the Old Italian violins. The instrument possesses a beautiful, colorful sound, rich in overtones.
What was missing all these years was the ability to make instruments with rich sound qualities and gorgeous varnish, equal to the Old Italian master- pieces. Only when we know how to make the second—varnish—will we be able to create the first –sound.
A violin made from the finest wood and constructed perfectly will not sound like a Stradivarius unless it also has similar varnish, applied with the same expert touch.
By studying Old Italian instruments, violinmakers could gather sufficient information about outline and arching, but the third critical variable, varnish, remained elusive. Varnish influences not only an instrument’s individual quality of sound, but also whether that sound, coaxed forth by competent players, will improve over time.
Having been able to replicate the design, it is now possible to complete the equation by re-establishing the tradition of cooking a marvelously simple soft varnish, which enhances the inherent qualities of every string instrument and allows it to improve over time.